Budgeting and Schedule
Like any project, there were a few setbacks that created budget and time constraints. In managing these setbacks and keeping the timeline of the project on track, the project management skills of the group members were constantly tested. A breakdown of the budget and schedule for the project can be seen below.
Schedule
The project was to be completed in three phases: design, construction, and testing. These phases took place over the course of the school year and the project was concluded the last week before graduation. Although some phases overlapped, the Fall quarter was the design period, the Winter quarter was the construction period, and the Spring quarter was the testing period. Even the best-laid plans can go awry and this project was no different. Along the way, there were a few setbacks that ranged from ordered parts not showing up on time to complete redesigns of certain components that created time constraints within the project. The Gantt Chart shown below offers an intensive look into the project schedule. There are seven main sections: Proposal/Report Writing, Analysis, Documentation, Part Manufacturing, Device Manufacturing, Device Evaluation, and Deliverables. The majority of the Fall quarter (the design period) was spent on sections 1-3: Proposal/Report Writing, Analysis, and Documentation. During this quarter, the team completed 12 engineering-based analyses, modeled and drew 10 components, as well as wrote the majority of the proposal. Although all design period deliverables were completed before the end of the quarter, managing the workload during this quarter proved quite difficult and a few late submission tokens were used. At the end of the Fall quarter, the engineers had a complete design that was ready to be manufactured. The Winter Quarter and the manufacturing phase consisted of sections 4 and 5: part manufacturing and device manufacturing. In this quarter, the car and its components were manufactured and assembled, with a final prototype finished at the end of the quarter. At the start of the Spring quarter, the project and the completed prototype entered the testing phase. This phase focused on sections 6 and 7: Device Evaluation and Deliverables. The Baja RC car underwent a multitude of tests to confirm the prototype met all design requirements and success criteria before finishing the proposal and delivering the final presentations. These tests included deflection tests, top speed tests, as well as competing in the CWU RC Baja competition at the end of the year. Upon completing the final tests and presentations, the project was concluded and the group members graduated!
​


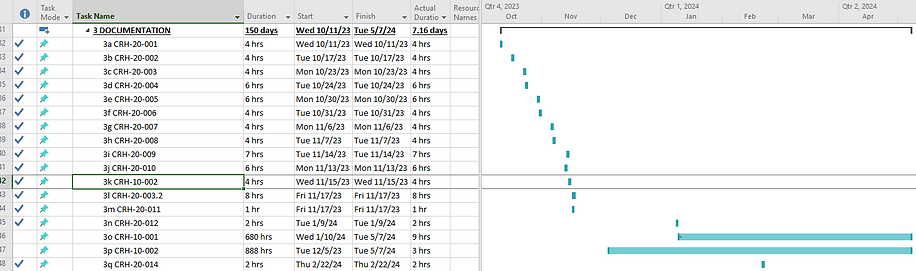

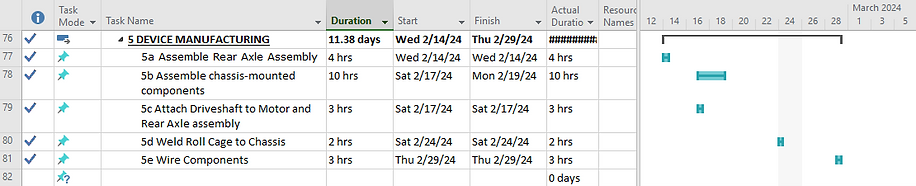


Figure 10
Budgeting
In deciding the ultimate budget for this project, the group members settled on a maximum of $1000 with a goal of only 75% of the budget being used. A breakdown of the budget and the individual items can be seen to the right (Table D1-Budget). Although the budget breakdown includes manufacturing and engineering labor costs, these costs can be ignored considering this was a senior project and the group members worked for free. Excluding the labor costs, the majority of the budget went towards purchased parts. Expensive one-off items such as the motor, electronic speed controller, battery, and driveshaft accounted for a large portion of the purchased parts section of the budget and were purchased during the Fall quarter. The cost for fasteners, bearings, and gears quickly added up over the course of the manufacturing process and accounted for the rest of the purchased parts cost. As seen in the table, the cost for materials included PLA plus, mild steel, aluminum, and stainless steel rods. These materials were used in the creation of all in-house manufactured parts.
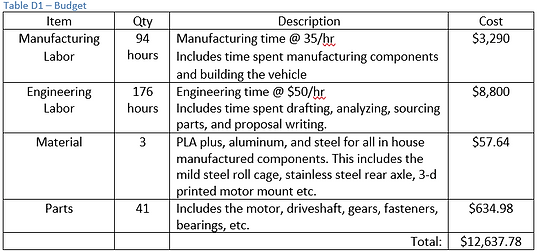