CWU RC Baja: Drivetrain and Chassis
​
Intro
Welcome to the big leagues, kid. This website is dedicated to showcasing the designing, manufacturing, and testing work that went into creating a drivetrain and chassis prototype to compete in the Central Washington University Remote-Control Baja Competition. Engineering principles such as statics, dynamics, kinematics, mechanics of materials, fatigue analysis, and mechanical design guided the design of the vehicle. Throughout the lifespan of the project, the vehicle went through a multitude of designs until finally narrowing in on the ultimate Baja RC car design. This website highlights the various aspects of the design process as well as the results of the project and tips for future mechanical engineers.
Spring Presentation: Final Presentation
Fall Presentation: Design
Winter Presentation: Working Device
Manufactured Vehicle
Rear-wheel drive, independent front suspension, trailing arms to solid rear axel, no differential
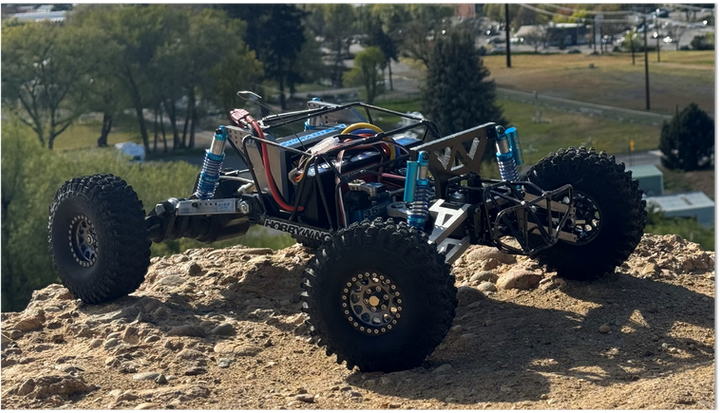
Final Product
The photo above depicts the car in all its glory atop Craig's Hill in Ellensburg Washington. Team member Chayce Williams took this photo days after the end-of-year competition and top speed test had taken place. The front bumper is deformed from a high speed impact with a curb but the chassis and drivetrain remained structurally sound and operational.
Figure 0
Figure 17

Figure 2

Figure 1
Alternate Design 1
Independent front and rear suspension, true differential
Initial Sketch
Rear-wheel drive, independent front suspension, trailing arms to solid rear axel, no differential
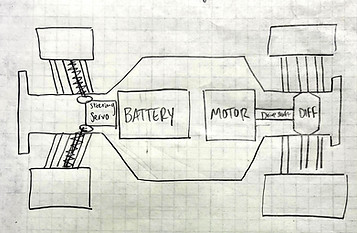
Figure 3
Alternate Design 2
Independent front suspension, trailing arms to back axle, true differential
Engineering Report PDF
Results
Table 2 - RC Baja Results

Overall, this project can be considered a success. Of the three major test requirements, the RC car prototype successfully passed each one. The chassis was more than 7x more rigid than the minimum requirement while remaining lightweight enough to allow the car to achieve the top speed and acceleration requirements. Although the top speed reached by the vehicle was lower than expected, the minimum speed of 20 MPH was achieved. The prototype was able to accelerate to 23 MPH in 5 seconds meaning the gear ratio chosen for the drivetrain balanced the top speed and torque effectively. While the vehicle's high center of gravity resulted in issues related to controllability at high speeds, the drivetrain was successful in powering the car towards achieving the velocity and acceleration requirements as well as winning first place in the end-of-year competition. Although the car got second in the slalom event and technically fourth in the drag race (second fastest car overall but got fourth in points), the car killed it in the Baja competition and was the only vehicle to last the entire day with no broken components.
​
The results shown in the table above are a great representation of the car's capabilities. The chassis deflection test was conducted on an Instron 34SC-E and simulated in Inventor Nastran. The results of the test and simulated model were extremely close meaning the test result can be considered accurate. As for the top speed of the vehicle, the team believes the value of 24 MPH undervalues the power of the drivetrain design given the issues related to controlling the vehicle at high speeds. The vehicle's steering setup was incredibly hard to keep straight meaning the vehicle wanted to run to the side while conducting the top speed and acceleration tests. The team had to conduct many trials to achieve successful and repeatable results in which the car drove in a relatively straight line. Although the top speed and acceleration requirements were achieved, the team believes these values misrepresent the full capability of the drivetrain design.