Analysis
In designing a solution to the engineering problem at hand, a multitude of analyses were performed to ensure the chassis and drivetrain prototypes would meet all success criteria. Almost every component on this vehicle correlates to an engineering analysis that determined the design parameters of that component. These analyses ranged from simple kinematics to statics and mechanics of materials and even fatigue analysis and failure modes. The photos below offer a surface-level introduction in to the types of analysis performed for this project.

Table 1 - Design Requirements
Analysis 1: RPM and Acceleration

In this analysis, the engineers related the outer diameter of the wheel to the required RPM and acceleration of the axle and driveshaft in order to hit the design requirements. By relating the circumference of the wheel to the minimum top speed of the vehicle, the engineers were able to determine a minimum RPM of 1680. At this RPM, the wheels are spinning at a speed that would result in the car travelling at 25 MPH and successfully hitting the 20 MPH top speed requirement. In addition to this, the engineers determined the minimum angular acceleration of the axle to meet the acceleration requirements. The analysis determined that the axle must accelerate at 35.19 rad/s in order to accelerate to 20 MPH in 5 seconds. These analyses were helpful in determining gear ratios and torque on the driveshaft and rear axle. They utilized kinematics and dynamics engineering knowledge.
Figure 4
Design Parameter: Minimum RPM of 1680 and Acceleration of 35.19 rad/s
Analysis 11: New Motor Gear Ratios and Kinematics
In this analysis, the engineers analyzed the newly purchased motor and the required gear ratios to satisfy the acceleration and top-speed design requirements. By multiplying the motor kv rating by 7.4 volts, the engineers were able to determine the maximum rpm of the motor. Using this value, the engineers then solved for the required rpm to achieve 35 MPH with 5-inch wheels. Using these two RPMs and dividing the input speed by the output speed, a suitable gear ratio was determined. Although a perfect gear ratio of 4.4028 : 1 was ideal, the group members found a pair of RC car upgrade gears online with a gear ratio of 4.3 : 1. Using these available gears, the engineers then recalculated the theoretical top speed of the motor using the available gears and were quite happy with the result.

Figure 5

Figure 6
Figure 9
Design Parameter: 4.3 to 1 bevel gear ratio and a top speed of 35.84 MPH
Analysis 2: Driveshaft Diameter
In this analysis, the engineers determined a minimum diameter of the driveshaft in order to handle a 20 lb. weight being hung from one end without surpassing the maximum deflection requirement. The analysis utilized a safety factor of 2.5 when determining the maximum deflection and after performing a cantilever beam deflection formula, resulted in a diameter of 0.3839". To simplify the manufacturing process, a diameter of 0.39" was chosen by the engineers. Although this design parameter was not a standard size, this part was to be machined by the engineers themselves meaning a standard size wasn't necessary. Additional analyses such as a shear-moment diagram, tensile stress calculation, and shear stress calculation were performed to make sure the part would pass the deflection test, but also succeed in handling the shear and tensile stresses inflicted upon it.


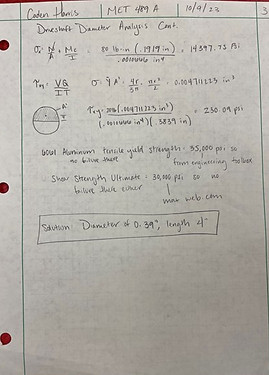
Figure 7
Figure 8
Figure 9
Design Parameter: Driveshaft Diameter of 0.39" and length 4"
Analysis 4: Rear Axle Diameter

